Gas Lift Manual by Gabor Takacs, unknown edition, Open Library is an initiative of the Internet Archive, a 501(c)(3) non-profit, building a digital library of Internet sites and other cultural artifacts in digital form. The Gas Lift Manual is a thorough, handy reference that is essential to the practicing engineer needing to successfully perform this type of artificial lift project. In his manual, Takacs imparts more than 30 years experience and research in the artificial lift methods arena. He starts the manual with an introduction to gas lift, and then moves. Gas Lift Gas Lift by Weatherford 6 years ago 4 minutes, 12 seconds 222,002 views A video introducing, gas, -, lift, theory and technology used in, artificial lift,. How to Not Stall a Manual Car - Clutch Control Tips and Tricks. Replace the burner base. See the following illustration for The surface grates interlock using the hook on one end of the grate burner positions. And the indent on the other. To remove the grates, lift the rear of the left grate off the hook, and then lift the front of the right grate off the hook and pull apart. Page 11: Cookware. A proper gas lift installation design, therefore, assures trouble-free operation for the entire productive life of a well. 1, 2 The usual gas lift installation types are classified in two broad categories: tubing flow and casing flow installations. In a tubing flow installation, lift gas is injected in the casing-tubing annulus,.
You must log in to edit PetroWiki. Help with editing
Content of PetroWiki is intended for personal use only and to supplement, not replace, engineering judgment. SPE disclaims any and all liability for your use of such content. More information
Ideally, an artificial-lift system should be chosen and designed during the initial planning phase of an oil field. However, in the haste to get a field on production, artificial lift may not be considered until after other production facilities are designed and installed. It is difficult to choose and install the optimum artificial-lift system after the surface production facilities have been installed. This is especially true in the case of gas lift.
- 2Factors having an effect on the design of a gas lift system
Fundamentals of gas for gas lift design
Only the gas fundamentals essential to the design and analysis of gas lift installations and operations are discussed in this section. The more important gas calculations related to gas lift wells and systems can be divided into these topics:
Factors having an effect on the design of a gas lift system
Most production equipment affects the design of a gas lift system, so it is best to design the gas lift system concurrently with the design of surface facilities. The entire purpose of a gas lift system is to reduce the bottomhole flowing pressure of the well. Anything that restricts or prevents this from occurring will have an impact on the system and must be considered in the design.
Field layout and well design

Consideration of gas lift operations should be a prime factor in sizing the hole for the desired oilwell tubulars. This is particularly true in offshore wells where all of the downhole gas lift equipment, except the valves, is installed during the initial completion. In on-shore fields, gas lift affects the size and location of gathering lines and production stations. Artificial lift should be considered before a casing program is designed. Casing programs should allow the maximum production rate expected from the well without restrictions. Skimping on casing size can ultimately cost lost production that is many times greater than any savings from smaller pipe and hole size. The same is true in flowline size and length. Production stations should be relatively near the producing wells. In most cases, increasing the size of the flowline does not compensate for the backpressure generated by the added pipe length. Any item of production equipment that increases backpressure at the wellhead, whether it be wellhead chokes, small flowlines, undersized gathering manifolds and separators, or high compressor suction pressure, seriously impacts the operation of a gas lift system. Fig. 1 illustrates the effect of backpressure on injection-gas requirement and fluid production in a 6,900-ft gas lift well.[1]
Fig. 1-Effect of wellhead backpressure on daily production rates and injection-gas requirements.[2]
Injection-gas pressure
Choosing a proper injection-gas pressure is critical in a gas lift system design. [2] Several factors may affect the choice of an injection-gas pressure. However, one primary factor stands out above all others. To obtain the maximum benefit from the injected gas, it must be injected as near the producing interval as possible. The injection-gas pressure at depth must be greater than the flowing producing pressure at the same depth. Any compromise with this principle will result in less pressure drawdown and a less efficient operation. High volumes of gas injected in the upper part of the fluid column will not have the same effect as a much smaller volume of gas injected near the producing formation depth because the fluid density is reduced only above the point of gas injection.

Gas Lift Design
The equilibrium curve[1] illustrates the effect of injection-gas depth on a particular well. The equilibrium curve is established by determining the intersection of the formation-fluid pressure gradient below the depth of gas injection with the produced gas lift gradient above the depth of gas injection for various producing liquid rates (See Fig. 2). In Fig. 2, the intersections of the flowing formation-fluid pressure-gradient traverses for a 400-B/D rate and a 600-B/D rate with the flowing total (formation plus injection gas) -pressure-gradient traverses above the point of gas injection to the surface for both rates are shown. If intersections are established for a large number of rates, as are shown in Fig. 3, the points can be connected and will form what is referred to as an equilibrium curve. When injection-gas pressure traverses are drawn from the surface, it is possible to determine the maximum gas lift rate from the well for various surface injection-gas pressures. Referring again to Fig. 3, a 1,200-psig surface injection-gas pressure would gas lift this well at a rate slightly above 600 B/D.
Fig. 2-Construction of an equilibrium curve.
Fig. 3-Complete equilibrium curve for specific well conditions.
Less downhole equipment may be required when higher injection-gas pressures are used (see Fig. 4). The higher injection-gas pressure provides a greater pressure differential between the injected-gas pressure and the flowing tubing pressure; thereby, allowing a greater spacing between valves. Thus, fewer mandrels and valves are required to reach the maximum injection-gas depth. Note that in Fig. 4, the 800-psig design reaches only the depth of 4,817 ft and requires seven gas lift valves. In comparison, the 1,400-psig design uses only four gas lift valves to reach the full depth of the well at 8,000 ft. The maximum pressure drawdown at the formation with the 800-psig injection gas is only 210 psi (2,200 to 1,990) compared to 1,010 psi (2,200 to 1,190) when 1,400-psig injection gas is used.
Fig. 4-A graphical design for a continuous-flow gas lift installation based on 800-psig injection-gas pressure (light lines) overlaying a design for 1,400-psig injection-gas pressure.
Gas Lift Manual Gabor Takacs
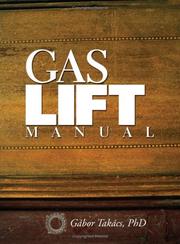
Major factors that have an effect on choosing the most economical injection-gas pressure
Only the basic conditions that must be met to ensure the most efficient injection-gas pressure to maintain operating pressure for a given well have been discussed. A variety of other factors can affect the selection of the most efficient surface injection-gas pressure. These may include:
- Pressure/volume/temperature (PVT) properties of the crude
- Water cut of the producing stream
- Density of the injected gas
- Wellhead backpressure
- Pressure rating of the equipment
- Design of the well facility
Calculating the effect of injection-gas pressures on surface production facilities
The selection and design of compression equipment and related facilities must be closely considered in gas lift systems because of the high initial cost of compressor horsepower and the fact that this cost usually represents a major portion of the entire project cost. In most instances, the injection-gas pressure required at the wellhead determines the discharge pressure of the compressor. Higher injection-gas pressures increase the discharge pressure requirement of the compressor, which is translated into a related increase in the compressor horsepower required for a given volume of gas. However, if the gas lift system is designed properly, the related decrease in gas volume requirements will result in an improvement in overall operating efficiency.
Gas volume
The total injection gas required for a continuous-flow gas lift well may be determined by well-performance prediction techniques. Well-performance calculations are discussed later in this chapter, but they are typically obtained by simultaneously solving the well inflow and well outflow equations. Well inflow, or fluid flow from the reservoir, can be simulated by either the straight line pressure drawdown (PI) or the inflow performance relationship (IPR) methods. [3] Likewise, well outflow, or fluid flow from the reservoir to the surface, is typically predicted by empirical correlations such as those presented by Poettmann and Carpenter, [4] Orkiszewski, [5] Duns and Ros, [6] Hagedorn and Brown, [7] Beggs and Brill, [8] and others. Once typical gas volume requirements for individual wells are determined, totals for the entire field can be calculated.
Dynamic gas lift valve performance
The importance of gas lift valve performance in the design of a gas lift installation is primarily dependent upon the maximum required injection-gas rates through the gas lift valves to unload and gas lift a well. Dynamic testing of gas lift valves indicated a noticeable difference in the performance of the 1-in.- and 1.5-in.-OD gas lift valves. Although both OD of these gas lift valves had the same port size, the 1.5-in.-OD valve with the larger bellows had a much higher injection-gas throughput rate for the same increase in the injection-gas pressure above the initial valve opening pressure. For this reason, the larger-OD gas lift valve with a 0.77-in.2 bellows area is recommended for gas lifting high-rate wells with large tubing.
Camco Gas Lift Manual
In recent years, there has been considerable interest in the actual injection-gas throughput rates of gas lift valves. API RP 11V2[9] presents the recommended methods for testing gas lift valves. A single-element unbalanced gas lift valve has two fundamental characteristics that are determined from a probe test. The procedure for performing the probe test is outlined in RP 11V2. These characteristics are the bellows-assembly load rate or spring rate and the approximate effective linear travel of the valve stem. The required valve-stem travel to ensure a fully open port increases with the valve port size, as shown in Fig. 5, for gas lift valves with square, sharp-edged seats. If the maximum linear stem travel is less than required for a fully open port area, the injection-gas throughput will be less than the gas rate through an orifice with an area equal to the port area.
Fig. 5-Equivalent area of a gas lift valve port vs. stem travel based on the lateral surface area of the frustum of a right circular cone.
Gas lift design and operation can be divided into two categories on the basis of the primary opening force. If a valve is opened primarily by an increase in the injection-gas pressure in the casing, the valve is called an injection-pressure-operated gas lift valve. A production-pressure-operated valve is opened primarily by an increase in the flowing-production pressure in the tubing at valve depth.
The typical standardized bellows sizes are 0.31 in.2 for 1-in.-OD gas lift valves and 0.77 in.2 for the 1.5-in.-OD valve. There are other sizes of bellows and smaller-OD gas lift valves for special clearance applications that will not be included in this section. The OD of a gas lift valve does not ensure the bellows size. The 1.5-in.-OD gas lift valve may have a smaller bellows. The published specifications for a valve indicate the bellows size.
A gas lift valve should be tested in the exact same manner as it is operated in a well. Typical port sizes for 1-in.-OD gas lift valves are 1/8-, 3/16-, 1/4-, 5/16-, and 3/8-in. ID. Port sizes of 3/16-, 1/4-, 5/16-, 3/8-, 7/16-, and 1/2-in. ID are available for 1.5-in.-OD gas lift valves (See Table 1.). These injection-pressure-operated valves are opened by an increase in the injection-gas pressure being applied over a major portion of the effective bellows area. It is impractical to attempt to open these valves by increasing the flowing-production pressure that acts on a much smaller area. Theoretically, a several hundred or thousand psi increase is required to fully stroke these valves by only increasing the flowing-production pressure.
Api Gas Lift Manual
Table 1
Operators should recognize the possibility of limited injection-gas passage of gas lift valves for gas lifting high-rate wells through large tubing or casing annulus. An injection-gas throughput rate based on a fully open port size should not be assumed for the larger port sizes in many unbalanced, single-element gas lift valves. For the maximum actual range in the injection-gas pressure during typical gas lift unloading operations, the equivalent port area open for the injection-gas flow is less than an area based on the reported port size for gas lift valves with a large port area relative to the effective bellows area. Assuming that a 1-in. OD gas lift valve with a large port has the valve stem travel to fully open, the necessary increases in the injection-gas pressure to stroke the valve stem for this required travel may approach, or exceed, 200 psi for a constant flowing-production pressure. Maximum valve-stem travel may also be limited by manufacturing tolerances running in the same direction, a mechanical stop, or by the bellows stacking before a fully open port is achieved.
References
- ↑ 1.01.1Blann, J.R. and Williams, J.D. 1984. Determining the Most Profitable Gas Injection Pressure for a Gas Lift Installation (includes associated papers 13539 and 13546 ). J Pet Technol36 (8): 1305-1311. SPE-12202-PA. http://dx.doi.org/10.2118/12202-PA.
- ↑ 2.02.1Gas Lift, Book 6 of Vocational Training Series, third edition. 1994. Dallas, Texas: API, E&P Dept.
- ↑Vogel, J.V. 1968. Inflow Performance Relationships for Solution-Gas Drive Wells. J Pet Technol20 (1): 83–92. SPE 1476-PA. http://dx.doi.org/10.2118/1476-PA.
- ↑Poettmann, F.H. and Carpenter, P.G. 1952. The Multiphase Flow of Gas, Oil and Water Through Vertical Flow Strings. Drilling & Prod. Prac., 257.
- ↑Orkiszewski, J. 1967. Predicting Two-Phase Pressure Drops in Vertical Pipe. J Pet Technol 19 (6): 829–838. SPE-1546-PA. http://dx.doi.org/10.2118/1546-PA.
- ↑Duns, H. Jr. and Ros, N.C.J. 1963. Vertical Flow of Gas and Liquid Mixtures from Boreholes. Proc., Sixth World Petroleum Congress, Frankfurt, Germany, Sec. II, Paper 22-PG.
- ↑Hagedorn, A.R. and Brown, K.E. 1964. The Effect of Liquid Viscosity in Two-Phase Vertical Flow. J Pet Technol 16 (2): 203-210. SPE-733-PA. http://dx.doi.org/10.2118/733-PA.
- ↑Beggs, D.H. and Brill, J.P. 1973. A Study of Two-Phase Flow in Inclined Pipes. J Pet Technol25 (5): 607-617. SPE-4007-PA. http://dx.doi.org/10.2118/4007-PA.
- ↑ API RP 11V2, Recommended Practice for Gas Lift Valve Performance Testing, first edition. 1995. Washington, DC: API.
Noteworthy books
Brown, K. E. (1967): GAS LIFT THEORY AND PRACTICE. Petroleum Publishing Co., Tulsa, Oklahoma.
Hernandez, A. (2016): FUNDAMENTALS OF GAS LIFT ENGINEERING. ISBN 978-0-12-804133-8 Gulf Professional Publishing, Cambridge, MA, 966p
Takács G. (2005): GAS LIFT MANUAL. ISBN 0-87814-805-1 PennWell Books, Tulsa Oklahoma, 478p.
Noteworthy papers in OnePetro
Use this section to list papers in OnePetro that a reader who wants to learn more should definitely read
External links
Use this section to provide links to relevant material on websites other than PetroWiki and OnePetro
See also
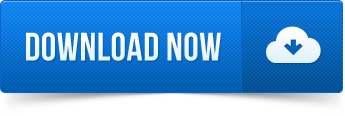